ECO.PROFILE – Nachhaltige Extrusion
Realisierung eines innovativen Verfahrens zur Steigerung des Rezyklatanteils und Verbesserung der Ressourceneffizienz bei der Extrusion von Kunststoffprofilen.
Umweltentlastung
Umweltentlastung
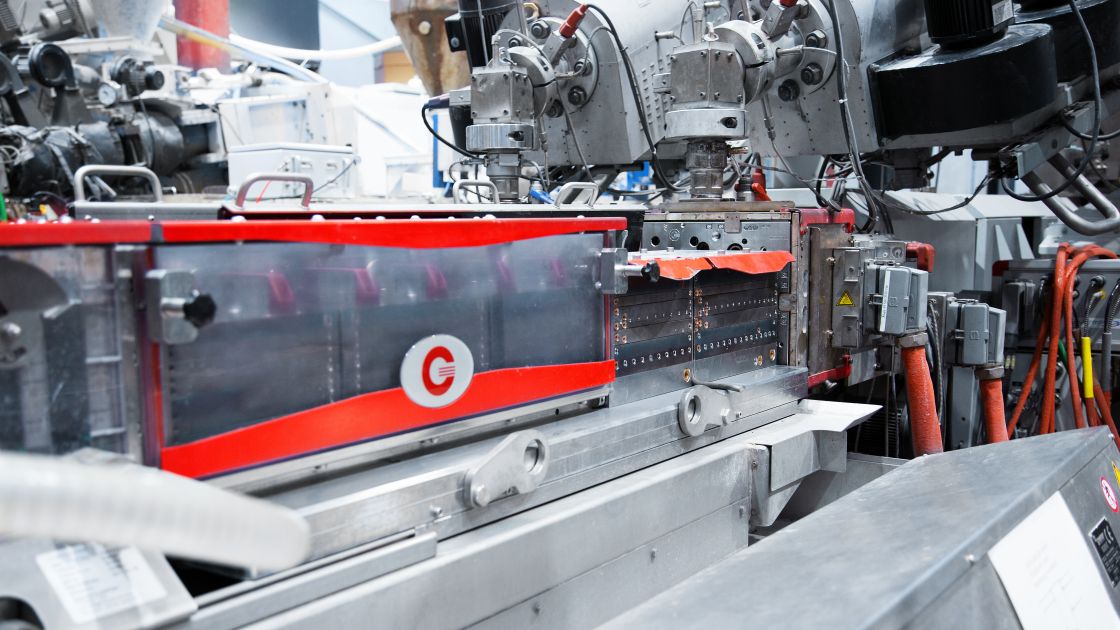
Kurzbeschreibung
Das Familienunternehmen aluplast GmbH, gegründet 1982 in Ettlingen bei Karlsruhe, zählt zu den führenden Anbietern von Kunststoff-Profilsystemen, wobei eine nachhaltige und ressourceneffiziente Produktion im Fokus bei unternehmerischen Entscheidungen steht. Das Unternehmen beschäftigt heute 1.900 Mitarbeiter weltweit und gilt als Innovationsführer in der Branche.
Grundsätzlich wird im Bereich der Kunststoffextrusion von Fenster-, Tür- und Rollladenprofilen insbesondere hochwertiges Polyvinylchlorid (PVC) eingesetzt, welches sich durch eine hervorragende Recyclingfähigkeit auszeichnet. Durch das Recycling von post consumer und post industrial Profilen können dabei nicht nur Primärstoffe eingespart sondern infolgedessen auch erhebliche Umweltentlastungen realisiert werden. Bei konventionellen Extrusionsanlagen ist jedoch der Einsatz von Rezyklaten insbesondere aufgrund der bislang erreichten Prozessstabilität limitiert, sodass eine Steigerung der Regranulatanteile zu überproportionalen Ausschussquoten führt.
Aufbauend auf dieser Problemstellung beim aktuellen Stand der Technik wurde im Rahmen des Investitionsvorhabens erstmalig das innovative ECO.PROFILE-Verfahren umgesetzt, welches hinsichtlich der erreichten Prozessstabilität neue Maßstäbe setzt. Darüber hinaus wurden entlang der gesamten Prozesskette umweltrelevante Innovationen realisiert, mit dem Ziel, die Ressourceneffizienz in der Extrusion grundsätzlich zu verbessern. Beispielhaft zu nennen sind an dieser Stelle ein für größere Rezyklatmengen ausgelegter Coextruder, eine exakte Abstimmung der einzelnen Prozessschritte, die Integration eines innovativen Werkzeug-Palettensystems sowie einer neuartigen Wasser-Luft-Trennung.
Im Vergleich zu einer konventionellen Extrusionsanlage konnte nach Umsetzung des Investitionsvorhabens der Rezyklatanteil bei Rahmenprofilen signifikant gesteigert werden. Die dabei erzielte Substitution von Primär-PVC entspricht ca. 1.200 Tonnen CO2-Äquivalenten, was den erheblichen ökologischen Stellenwert des Investitionsvorhabens unterstreicht. Darüber hinaus kann im Vergleich zum aktuellen Stand der Technik zukünftig der jährliche Energiebedarf sowie die Ausschussquote erheblich reduziert werden. Da das ECO.PROFILE-Verfahren des Weiteren einen neuartigen Wasserkreislauf vorsieht, kann auf den Einsatz von Bioziden sowie auf eine kontinuierliche Frischwasserzufuhr vollständig verzichtet werden.
Mit Umsetzung des Investitionsvorhabens hat die Firma aluplast aufgezeigt, dass Umweltschutz, Energieeffizienz und Nachhaltigkeit durch den Einsatz von innovativen Anlagen- und Lösungskonzepten bei gleichzeitiger Wirtschaftlichkeit realisiert werden können. Das Demonstrationsvorhaben definiert dabei einen neuen Branchenbenchmark, wobei innerhalb des Unternehmens als auch der Branche erhebliche Multiplikatoreffekte gegeben sind.