Investition in eine hochinnovative, ressourcenschonende Farbsprühanlage für Glasprodukte
Umweltentlastung
Umweltentlastung
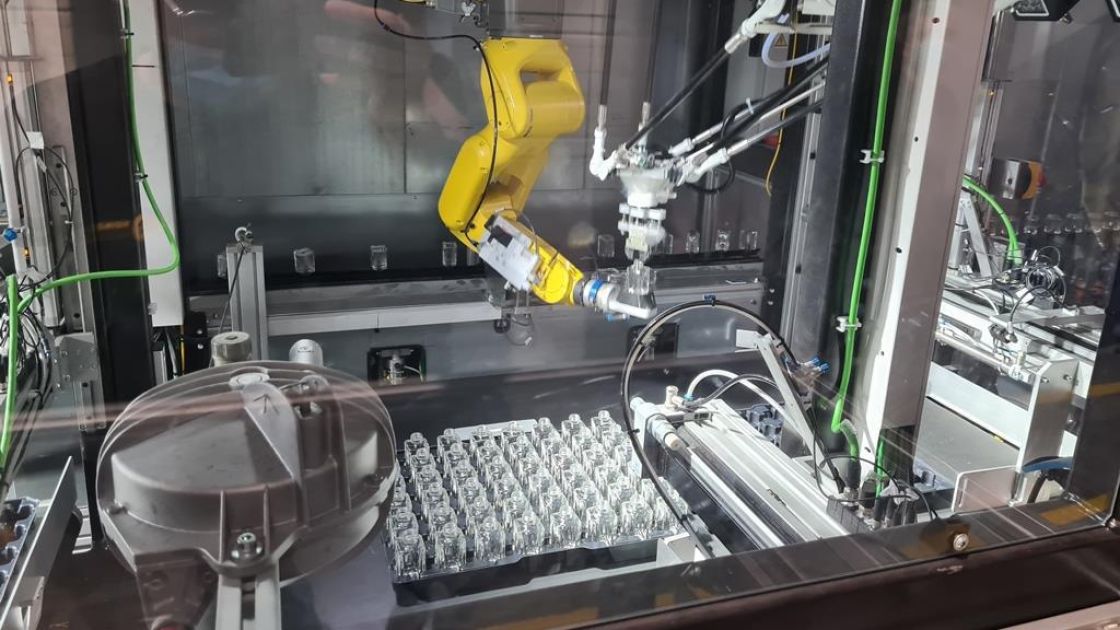
Kurzbeschreibung
Die Heinz Glas Group stellt Parfumflakons her und die Heinz Veredelungs GmbH & Co. KGaA veredelt diese Glasflakons in vielfältigen Variationen. Dies ist ein komplexer Vorgang, der unter anderem durch das vorgegebene Design der Flaschen (Form und Farbgebung) beeinflusst wird. Die Vielzahl der verschiedenen Glaskörper erfordert auch eine maximale Flexibilität sowie häufige Produktwechsel. Die verschiedenen Geometrien und Farbeffekte erfordern den Einsatz von bis zu 12 verschiedenen Sprühpistolen. Die Flakons werden hierzu auf rotierenden Stäben aufgebracht, mittels Vorbehandlung automatisch von Staub befreit und anschließend an Sprühpistolen vorbei geführt. Die Rotation sowie die präzise Einstellung der Pistolen führen zu einem gleichmäßigen Farbauftrag. Anschließend werden die besprühten Flakons ca. 15-25 Minuten durch einen Trocknungsofen geführt. Um einen optimalen Farbauftrag und komplexe Muster gewährleisten zu können, bedarf es einer hohen Prozessstabilität sowie erfahrener Mitarbeiter, die die Flacons auf den rotierenden Stäben platzieren und die Sprühpistolen optimal einstellen können.
Ziel des Vorhabens war die erstmalige großtechnische Anwendung eines innovativen Veredelungssystems für Glasflakons mit automatisierter Anlagebestückung und Sprühpistoleneinstellung sowie teilweise Infrarot-beheiztem Ofen zur besseren Ansteuerung der zu beheizenden Areale. Durch den Einsatz eines Roboters zur Bestückung der Anlage mit Flakons können diese so präzise platziert werden, dass der nachfolgende Farbauftrag optimal erfolgt. Die automatisierte Einstellung der Sprühpistolen führt dazu, dass die manuellen Einstellzeiten und damit verbundenen Ausschussquoten sowie Leerlaufzeiten des Trockenofens erheblich reduziert werden konnten. Der Trockenofen selbst ist auch erheblich energieeffizienter und kann durch die Infrarottechnologie (IR-Technologie) die Wärme gezielter an die entsprechenden Stellen des Flakons bringen, so dass der Energiebedarf deutlich gesenkt werden konnte. Durch den Einsatz der IR- Technologie konnte somit der Umrüst- und Anfahrprozess erheblich verkürzt und effizienter gestaltet werden.
Durch die Implementierung und Vernetzung der einzelnen Technologien konnten jährlich, je nach Auftragslage ca. 7,7 Tonnen (>10 Prozent) Farben und ca. 150 Tonnen CO2 (12 Prozent) bei einer Produktionssteigerung von 20 Prozent eingespart werden.
Durch dieses Projekt konnte erstmals eine vollautomatisierte Oberflächenveredlung von Glasflakons großtechnisch realisiert werden, die auch auf andere vergleichbare Beschichtungsbedürfnisse übertragbar ist.