Errichtung einer umweltfreundlichen Schälmaschine
Innovative Schälmaschine ermöglicht energie- und materialeffiziente Produktion von geschmiedeten Rundstangen aus hochwertigen Sonderlegierungen.
Umweltentlastung
Umweltentlastung
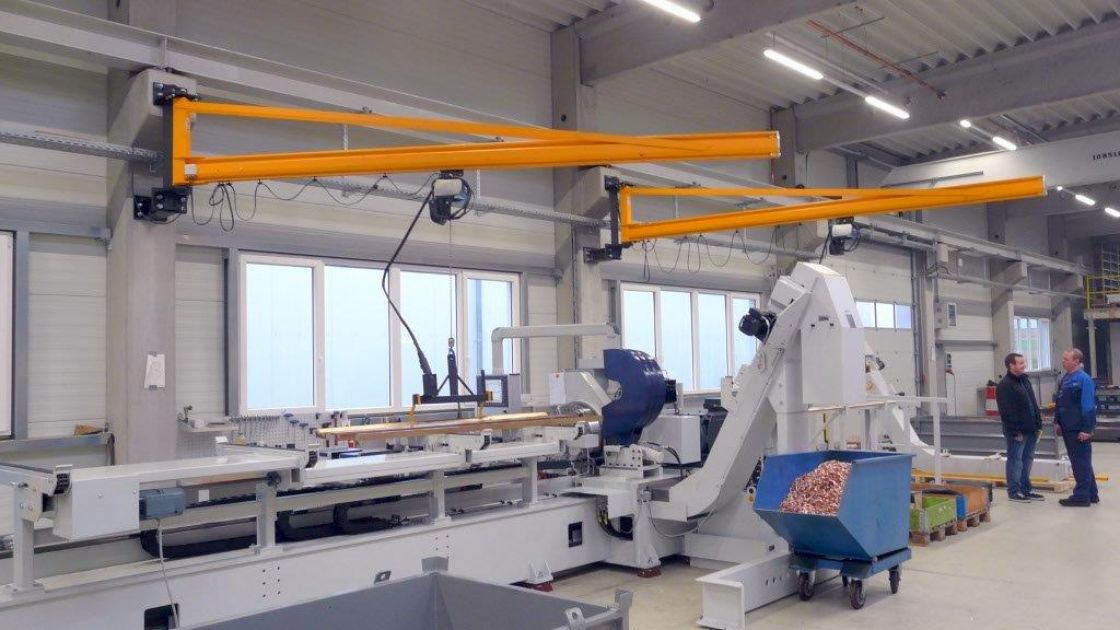
Kurzbeschreibung
Die Schmelzmetall Deutschland GmbH in Steinfeld-Hausen produziert u.a. Halbzeuge wie Rundstangen aus Sonderlegierungen auf Kupferbasis.
Nach dem derzeitigen Stand der Technik ist es, je nach geforderter Sonderlegierung und Durchmesser, entweder gar nicht oder nur unter hohem Energie- und Materialaufwand möglich, geschmiedete Rundstangen in kleinen Durchmessern kleiner als 3,5 Zentimeter herzustellen. Sofern möglich, müssen diese Rundstangen kleinen Durchmessers aus geschmiedeten Rundstangen größeren Durchmessers gedreht werden. Dabei geht dem Produktionsprozess ein Großteil des hochwertigen Materials in Form von Spanschrott verloren. Da die Späne mit Kühlschmiermitteln kontaminiert sind, werden sie im Recyclingwerk mit anderen Kupferschrotten vermischt und unspezifisch eingeschmolzen, was zum Verlust der hochwertigen Sonderlegierungen, wie Kobalt, Nickel oder Beryllium, führt.
Das Ziel des Vorhabens war die Installation einer neuartigen Schälmaschine zur bedarfsgerechten Produktion von geschmiedeten Rundstangen aus hochwertigen Sonderlegierungen, auch in kleinen Durchmessern.
Durch das neue Verfahren können aus einer geschmiedeten Platte bis zu 50 Vierkantstangen gesägt und anschließend zu Rundstangen geschält werden. Der Materialverlust beim Schälprozess ist im Vergleich zur Ausgangslage deutlich geringer. Zudem kommt beim neuen Verfahren erstmals eine Luft-Trockenkühlung anstelle einer Nasskühlung zum Einsatz, die ein legierungsspezifisches Recycling der nun unkontaminierten Späne ermöglicht.
Neben den Materialeinsparungen wird durch den neuen Prozess auch deutlich weniger Energie in Form von Strom für die Schmiedepresse und Erdgas für die Rekuperator-Öfen benötigt.
Beim Schmieden werden 66 Prozent weniger elektrischer Strom und 67 Prozent weniger Erdgas verbraucht. Bei Vollauslastung entspricht dies einer maximalen CO2-Einsparung von 193 Tonnen pro Jahr. Durch den Wegfall der Transportwege zur externen Bearbeitung an verschiedenen Standorten können zusätzlich bis zu 37 Tonnen CO2 eingespart werden.
Zudem bewahrt die Getrennterfassung unkontaminierter Sonderlegierungsspäne jährlich
- 458 Kilogramm Beryllium (gesamt)
- 398 Kilogramm Kobalt (gesamt)
- 446 Kilogramm Nickel (gesamt)
vor dem Downcycling (dissipativer Verlust der Legierungselemente).
Zudem werden durch die Trockenkühlung jährlich ca. 3.600 Liter Kühlschmiermittel eingespart.
Das Vorhaben besitzt einen guten Modellcharakter. Die Technik ist für alle Betriebe der metallverarbeitenden Industrie interessant - insbesondere für Betriebe, die Sonderlegierungen verarbeiten.