Innovative energieeffiziente Branntkalk-Mahlanlage: Horizontal-Schichtrollenmühle
Umweltentlastung
Umweltentlastung
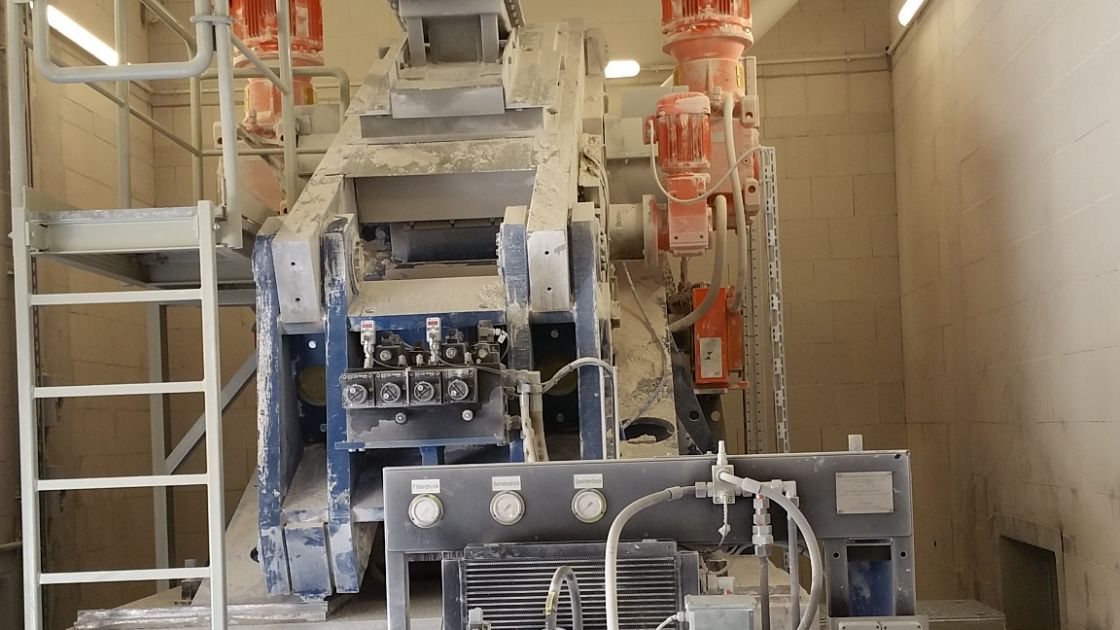
Kurzbeschreibung
Die Calcis Warstein GmbH & Co. KG veredelt aus inländischen Lagerstätten Carbonatgestein. Aus diesem Gestein wird Branntkalk für den Einsatz in vielen Industriezweigen mit verschiedenen Einsatzbereichen, wie Wasseraufbereitung, chemische Industrie, Lebensmittel- und Stahlherstellung, hergestellt.
Der durch das Brennen von Kalkstein erzeugte Branntkalk muss anschließend für die jeweiligen spezifischen Produktanforderungen aufbereitet, d.h. gemahlen werden. Für diesen Mahlvorgang kommen üblicherweise Kugelmühlen zum Einsatz.
Mit dem Vorhaben soll erstmalig in der Kalkindustrie eine Horizontal-Schichtrollenmühle zum Einsatz kommen und die energieintensive Kugelmühle ersetzen. Horizontal-Schichtrollenmühlen werden derzeit schon erfolgreich in anderen Industriezweigen, wie der Glas- und Zementindustrie, eingesetzt. Für die Kalkindustrie eigneten sich diese Mühlen bisher aufgrund der geringen Härte des Branntkalks nicht. Es bildeten sich festgepresste Materialmassen (Schülpen), die einen zusätzlichen Zerkleinerungsvorgang erforderlich gemacht hätten.
Die Technologie wurde weiterentwickelt, so dass auch Branntkalk ohne die unerwünschte Schülpenbildung und in ausreichender Materialqualität in Horizontal-Schichtrollenmühlen aufbereitet werden kann.
Mit dem Vorhaben können im Vergleich zum Stand der Technik (Kugelmühle) der Energieverbrauch um bis zu 40 Prozent und die Lärmemissionen um bis zu 90 Prozent gesenkt werden. Die Materialausbeute erhöht sich um bis zu vier Prozent. Außerdem können noch produktionsspezifische Hilfsmittel und die Erschütterungen im Umkreis der Anlage deutlich reduziert werden. Das CO2-Minderungspotenzial beträgt ca. 570 Tonnen pro Jahr.