Innovatives, energieeffizientes Patentier- und Verzinkungsverfahren für die Behandlung von Stahldrähten bei der Herstellung von Stahlseilen
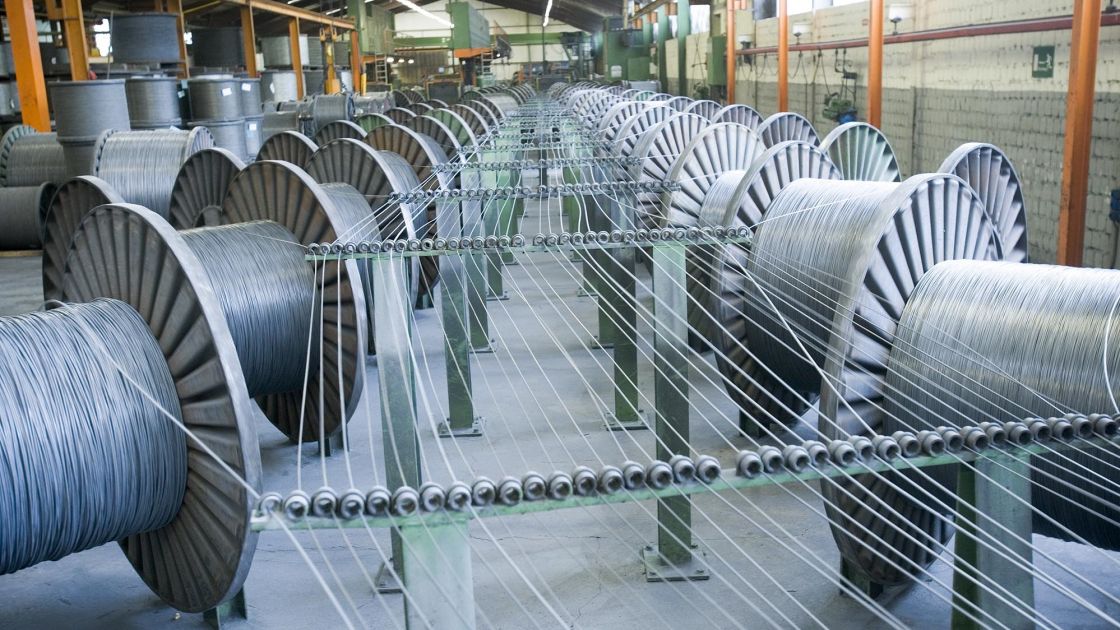
Kurzbeschreibung
Seit über 125 Jahren produziert die Vornbäumen Stahlseile GmbH & Co. KG in der eigenen Drahtzieherei und Seilerei Drähte und Stahlseile, die weltweit unter anderem in der Automobilindustrie, für Kräne, Aufzüge, Bagger und Seilbahnen eingesetzt werden. Die Herstellung von Stahlseilen ist ein komplexer Fertigungsvorgang, der rund zehn unterschiedliche Fertigungsschritte, wie mehrfache Wärmebehandlung der Drähte, chemische Vorbehandlung (Beizen und Fluxen), mehrstufiges Ziehen der Drähte auf das Endmaß sowie das Beschichten durch Feuerverzinkung, umfasst. Mit den Prozessschritten Vorzug, Patentierung und Verzinkung erfordert die Drahtbearbeitung erhebliche Mengen an Energie und Rohmaterialien.
Ziel des Demonstrationsprojekts war es, die Material- und Energieeffizienz der Drahtbearbeitung deutlich zu verbessern. Bei der neuen Patentieranlage für die Wärmebehandlung von Drähten sollte durch eine präzise, kontinuierliche Temperaturmessung mit einer Infrarot-Kamera die Verweilzeit der Drähte in dem Patentierofen genauer geregelt und die Beheizung optimal eingestellt werden. Geplant war, dadurch die Produktqualität zu steigern und den Erdgasverbrauch zu senken. Zudem sollte durch Schutzgaseinsatz im Ofen sowie auf dem weiteren Transportweg der Drähte die Oxidation (Verzunderung) der Drähte vermieden und auf das Beizen vor der Verzinkung verzichtet werden. Darüber hinaus sollte mit einer Stickstoff- oder Druckluftabstreiftechnik der Zinkauftrag auf den Draht optimiert und der Zinkeinsatz reduziert werden.
Im Zuge der Vorhabenumsetzung hat sich herausgestellt, dass es bei vollständiger Vermeidung der Oxidschicht auf den Drähten zu erheblichen Bleianhaftungen am Draht kommt. Diese resultieren aus der notwendigen Abkühlung der Drähte in einem Bleibad. Nur mit einer dünnen Oxidschicht auf der Drahtoberfläche war es möglich, bleifreie, weiterverarbeitungsfähige Drähte zu erhalten. Diese Oxidschicht führte allerdings zu einer schlechten Zinkhaftung, so dass das Beizen vor der Verzinkung nicht, wie geplant, entfallen, jedoch der Säureeinsatz um 25 Prozent gesenkt werden konnte. In der Folge konnte auch auf das Fluxen der Drähte vor dem Eintauchen in das Zinkbad nicht verzichtet, dafür aber die Einsatzmenge deutlich reduziert werden (um 23 Prozent geringerer Fluxmitteleinsatz).
Trotz der vorgenannten Änderungen bei der Umsetzung des Vorhabens wurden die erwarteten Energieeinsparungen erreicht und übertroffen. So ist der spezifische Stromverbrauch für die Drahtverarbeitung mit der Umsetzung des Vorhabens von 287 Kilowattstunde Strom pro Tonne Draht um 43 Prozent auf 163 Kilowattstunde pro Tonne gesunken, der spezifische Erdgasverbrauch von 505 Kilowattstunde Erdgas pro Tonne Draht um 28 Prozent auf 363 Kilowattstunde pro Tonne.
Bezogen auf die direkt und indirekt mit der Drahtverarbeitung verbundenen CO2 -Emissionen wurde das Vorhabenziel einer 30-prozentigen Minderung erreicht. So sind die spezifischen CO2-Emissionen von 368 Kilogramm CO2 pro Tonne Draht auf 256 Kilogramm CO2 pro Tonne Draht gesunken. Die absolute Menge der CO2-Emissionen ist mit Umsetzung des Vorhabens um 793 Tonnen gesunken. Den größten Beitrag zur Minderung der CO2-Emissionen (46 Prozent) hat dabei die Stromeinsparung beim Grobzug mit der induktiven Hochfrequenz-Drahttrocknung erbracht; danach folgen der neue Patentierofen mit der innovativen Steuerungstechnik (25 Prozent) sowie die Abwärmenutzung im Bonder- und Beschichtungsbad (14 Prozent der Gesamtminderung).