EPPI: Energieeffizienter Prozess zur Herstellung von hochreinem Isobuten
Umweltentlastung
Umweltentlastung
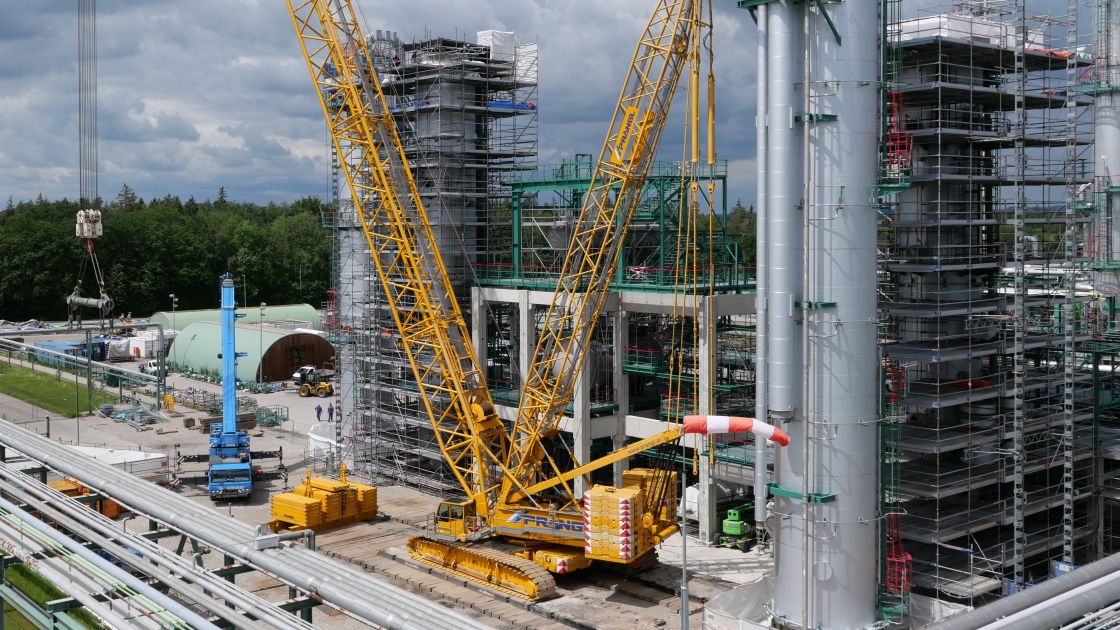
Kurzbeschreibung
Die OMV Deutschland GmbH (kurz: OMV) betreibt im bayerischen Burghausen eine Raffinerie zur Herstellung von petrochemischen Produkten, wie Propylen, Ethylen, Butadien und Mineralölprodukten (Diesel, Heizöl und Kerosin). Jährlich werden am Standort rund 3,8 Mio. Tonnen Rohöl verarbeitet.
OMV hat innerhalb der Petrochemischen Anlagen ein Isobuten reiches Nebenprodukt identifiziert, dass sich für die Aufbereitung und Herstellung von hochreinem Isobuten eignet. Der bisher bekannte Prozess, Isobuten über einen Zwischenschritt der Etherbildung und Spaltung zu gewinnen, ist mit einem erheblichen apparativen und energetischen Aufwand verbunden. Daher entwickelten OMV und BASF ein neues Verfahren, das eine wesentlich vereinfachte Prozessführung bedeutet und durch das niedrige Energie-Niveau die Möglichkeit bietet, vorhandene Prozesswärme aus einer bestehenden Anlage zu verwenden. Für die Entfernung der kritischen Komponenten erforderliche chemische Umwandlung entwickelte BASF einen sehr selektiven Isomerisierungsreaktor.
Es entstand somit ein Prozess, der aus einer chemischen Umwandlung (Isomerisierung) und anschließender Destillation besteht. Mehr als 80 Prozent der Wärme-Energie wird dabei über direkte Wärmintegration mit einer vorhandenen Kolonne gedeckt. Es war daher im ersten Schritt die Entwicklung des Prozesses und die Integration des Wärmeverbundes zu bewältigen. Dabei musste die neue Destillationskolonne so ausgelegt werden, dass der Energietransfer aus der bestehenden Prozesswärme gesichert für den neuen Bedarf zur Verfügung gestellt werden konnte und das Wärmepotential optimal genutzt werden kann. Für die Auslegung des Reaktors fanden bei BASF Versuche im Labor statt, bei denen Produkt aus der Anlage der OMV eingesetzt wurde.
Das so entwickelte Prozess-Design konnte in das Anlagenkonzept der OMV in Burghausen integriert werden. Es besteht in den wesentlichen Prozess Schritten aus Apparate-Typen (Reaktoren, Kolonnen, Wärmeaustauscher, etc.), die schon mehrfach bei OMV eingesetzt wurden. Daher waren die Auslegung des neuen Verfahrens und die Beschaffung und Montage ohne große technische Risiken möglich.
Die Anlage konnte wie geplant gebaut und in Betrieb genommen werden. Die Inbetriebnahme erfolgte in drei Schritten. Zuerst wurde der Isomerisierungsreaktor in Betrieb genommen, danach die Destillationskolonne und zum Abschluss die Wärmeintegration. Es konnten alle Prozess Ziele ohne Nachbesserung des Anlagendesigns erreicht oder sogar übererfüllt werden. Durch die erfolgreiche Wärmeintegration wurde der Bedarf an Energie, der über Dampf zur Verfügung gestellt werden muss, signifikant reduziert.
Somit konnte das Ziel der jährlichen CO2-Einsparung von 20.000 Tonnen erreicht werden. Durch Effizienzsteigerung an den Spaltöfen konnten jährlich zusätzlich ca. 5.000 Tonnen CO2 am Standort der OMV eingespart werden.
Das neue Verfahren konnte wie oben beschrieben bei der ersten großtechnischen Anwendung problemlos alle Erfolgskriterien erfüllen. Somit steht für weitere potenzielle Interessenten eine Referenz Anlage zur Verfügung, die für weitere Anwendungen positive Impulse setzen kann. Dabei stehen in erster Linie Petrochemische Anlagen im Fokus, die eine hohe Ähnlichkeit mit der bei OMV in Burghausen in Betrieb befindlichen Technologien hat, also z.B. Ethylen Anlagen. Es sind derzeit in Deutschland 10 Anlagen und europaweit ca. 40 Anlagen dieses Typs in Betrieb.